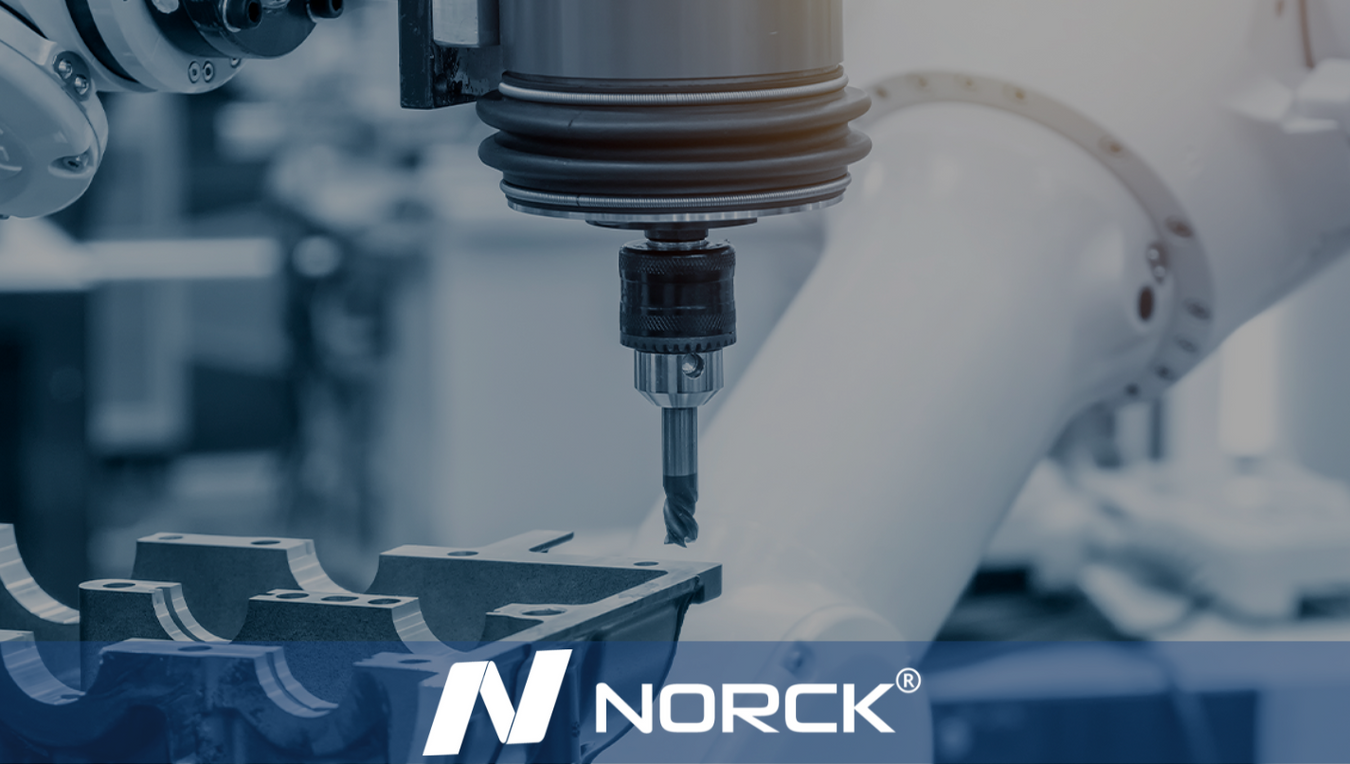
Precision Component Manufacturing with CNC Machining
Unlock the vast mount of CNC machining capacity with Norck for custom component manufacturing, precision metal and plastic manufacturing.
This guide will help you prepare your CNC machining parts for manufacturing.
Design for manufacturing, known as DFM, ensures that the components you design can be manufactured, which is crucial for outsourcing. It helps reduce the revisions and turnarounds.
Material Selection: Norck offers a large selection of CNC machining materials :
|
Material |
Accuracy (mm) |
Metals |
Titanium |
|
Stainless steel |
|
|
Still alloy |
|
|
Brass |
|
|
Copper |
|
|
Plastics |
Delrin (POM) |
|
PEEK |
|
|
ABS |
|
|
CPVC |
|
|
Acetal |
|
|
HDPE |
|
|
LDPE |
|
|
Polycarbonate (PC) |
|
|
Polypropylene (PP) |
|
|
PVC |
|
|
PS |
|
|
PSU |
|
|
PPSU |
|
|
PEI |
|
|
PET |
|
|
PMMA |
|
|
PTFE |
|
|
Nylon |
|
Finishes: We offer the finishes below for your CNC machining components :
- Assembling
- Riveting
- Powder coating
- Polishing
Technics of CNC machining: CNC machining designates different types of fabrication technics, but it mainly refers to CNC turning and CNC milling.
A. CNC milling:
CNC milling (Computer Numerical Controlled milling) designates a process that uses a rotating instrument to remove material from a workpiece.
B. CNC turning:
Contrary to CNC milling, where the rotating object is the instrument, in CNC turning, the workpiece rotates at high speeds to gain the needed velocity for the machining operation. In CNC turning,the workpiece is held into a lathe and spun at high speeds.
How to choose which process is more convenient for my product?
CNC turning is used when the desired shape is cylindrical or conical, while CNC milling is used when the desired shape is flat.
Choosing material: Material choice is crucial for a product'sfunctionality and aspect. Hard materials like titanium are more rigidbut will take more time to fabricate than soft materials,butmachining costs will be higher.
Shapes: In addition to material, the shape of parts can affect the project cost. Complex forms are more challenging to produce than primitive shapes.
A good solution is to divide the part with complex shapes into several parts. If a complex cavity is a must, wire EDM might be best for through all cavities, and EDM machining can form through all cavities like in molding cavities.
Accuracy: It is the deviation of the fabrication from the design. Afabricated partcan not be identical to the 3D model. the designer must add tolerances for acceptancecalled tolerance interval.
For example, a plate's thickness is 10mm, called nominal dimension. Adding tolerance interval to the nominal dimension of ±0.1mm means that any part with thickness from 9.9 to 10.1mm is considered acceptable.
Tight tolerances affectthe cost of parts, and large tolerances might affect their functionalities.
A good practice is analyzing parts' gaps and interference to determine the essential tolerances, and for non-functional features,applying large toleranceslowers the cost.
For example,inthe tolerancing system "ISO2768mk"the tolerance for a linear dimension of 5mm is ±0.1mm, which is a medium class. Amore coarsetolerance is ±0.05mm, large tolerance is ±0.3mm.
Our engineers can analyze your product and suggest the most cost-effective geometrical & dimensional tolerancing (GD&T) according to ISO and ASME standards.
Maximum size: We can manufacture parts as big as :
To ensure that your designed parts can be manufactured, you must keep the best practices to improve the manufacturability and get high-quality products.
Walls: Walls should be less than 0.5mm for metal and 1mm for plastic parts. If thin walls are a must, sheet metal might be a better alternative.
Cavities: Cavities are made by removing material from the raw parts. Due to the tool's length, the depthof cavitiesis limited to four times their width.Deep cavities affect the part cost as they take more time to manufacture and require special tooling.
Square corners: A square corner is the intersection of three edges in a cavity. CNC machining can't produce square corners. The solution is to add fillets to the edges, as shown below. The recommended radius should be 1/3 the depth of the cavity or greater.
If adding a fillet is not possible, you might use EDM machining.
Another recommended solution is to add dog-bone corners as shown below:
Corners: Add fillets to external vertical edges results in less stress accumulation, safer for assembly, and more aesthetic.
Chamfers: Add chamfers to help assemble parts and to break sharp edges.Avoid adding chamfers for all sharp edges. At Norck, we will break all sharp edges unless specified otherwise.
Undercuts: Undercuts are cavities that are not accessible in general and require special tooling, resulting in higher costs. We recommend dividing the part into several parts to facilitate the machining.
Feature height: The recommended height of a feature is four times its width.
3D profiles: 3D profiles are machined according to the 3D model definition. It is a complex shape that takes time to program and machine,adding to the part's cost. We recommend using simple forms instead if possible.
Holes: Hole depth can reach 30 times its nominal diameter, unlike cavities.
The standard diameters of holes range from 1mm to 38mm. Holes from 0.05 to1mm arefeasible, but the parts'cost will increase.
Threads: We offer tapping starting from #0-80 (ANSI) and M2 (ISO).The recommended depth of threads is three times the nominal diameter.
Unlock the vast mount of CNC machining capacity with Norck for custom component manufacturing, precision metal and plastic manufacturing.
Whether you need 3D-printed parts in plastic or metal, Norck has the right capacity and solution for you.
Thousands of companies around the world rely on Norck's vast capacity and its extremely qualified capabilities to get their sheet metals fabricated.